探秘蜂巢能源“短刀”电池工厂
02
硬科技成就智能制造
蜂巢能源“短刀”产线,不仅是全球最先进的电池生产线,也是智能制造的典范。
首先,这个产线应用了很多电池生产所需的高端装备。
最典型的就是超高速叠片机。在蜂巢能源一开始打出“叠时代”口号时,还是从韩国寻找先进的叠片技术和设备。但是二期即将启用的超高速刀片式电芯叠片机,就是蜂巢能源自己研发设计,委托设备厂加工的。
前面提到,这个叠片机叠片效率可以做到0.125s/片,超越普通卷绕工艺的效率,引领了全球叠片工艺的进步。
此外,在匀浆工序中,蜂巢采用了2300L大容量双行星搅拌设备。刘小安介绍,这个设备的单体容量在行业里是最大的,每罐浆料可生产纯电动车约10辆左右。
其次,这个产线大量应用了机器视觉,帮助实现工业自动化和智能化。
“短刀”产线主要用了三种机器视觉设备:β射线检测系统、激光检测和CCD(影像)检测。
β射线检测和激光检测是对检测对象发出β射线或者激光,通过检测β射线衰减情况或者是激光反射数据,来分析、测量检测对象的厚度、大小、位置等数据。
而CCD检测,就如同给被检测对象拍了一张照片,然后将图像信号转换为数字信号,再通过系统对信号进行运算,来判别被检测对象的特征。
蜂巢能源大量应用这些设备,来监测监测电芯生产品质。
比如在涂布工序上,蜂巢采用3套β射线在线面密度检测系统和2项CCD实时涂宽检测系统,来确保面密度的一致,以及涂布位置的准确性。
再比如,在辊压工序,蜂巢采用了实时在线激光测厚技术,帮助辊压厚度控制在±3微米以内。
还有,在模切工序上,蜂巢采用2套CCD检测极片的白点、黑点、划痕,以及尺寸是否符合要求。
对于人眼不能看出来的问题,机器的视觉可以做到无论巨细,都一览无遗,帮助把控产品质量。
叠片之前采用激光预定位
第三,蜂巢能源“短刀”产线大量采用了人工智能(AI)技术。
在蜂巢能源开始规划建厂时,就以建设车规级动力电池为标准,而要做到车规级,就必须大量采用AI技术。
AI要发挥作用,参照人类的智能,首先它要像人一样,能有感官来获取信息,因此,产线必须实现高度数字化,让人工智能充分掌握产线的信息。
蜂巢能源在这一方面,通过人、机、料、法、环、测、时间等7维制程管控,实现过程超过2500个因子的监控,并可追溯到单电芯每个制程的过程数据。这些数据在手,AI对产线就一览无遗了。
AI发挥作用的第二步,是学习。通过大数据的分析,AI逐步建立2500个因子的参数,和产品质量、数量的关系。这一过程中,蜂巢并不依赖它的供应商西门子,而是建立了自己的算法团队,通过构筑各种模型,来训练AI。
AI发挥作用的第三步,是智能反馈、持续调优。在找到各个因子和产品质量、数量关系之后,AI就能寻找最佳参数组合,来提升质量或者效率。
举例而言,在涂布工序中,β射线检测系统和CCD涂宽检测系统与涂布机是实时互动的。一旦检测设备发现了面密度和位置的异常,就会自动调整涂布参数,让涂布机执行,使其达到生产的要求。
当前,电池生产也已经成为不同企业、甚至不同国家争相布局的业务。设备的先进水平、智能化水平,则是判断电池工厂的两大标准。目前,蜂巢“短刀”工厂,智能制造水平是领先的。
特别是人工智能。先进的设备可以购置或者模仿学习,但是人工智能的布置和进化,需要时间和积累。
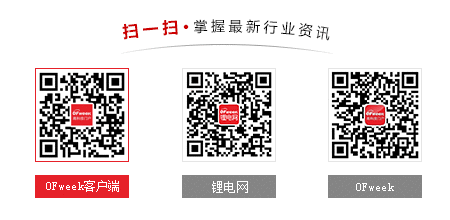
图片新闻
最新活动更多
-
11月14日抢先报名>> OFweek 2024固态电池技术线上研讨会
-
即日-11.30免费预约申请>>> 燧石技术-红外热成像系列产品试用活动
-
11月30日立即试用>> 【有奖试用】爱德克IDEC-九大王牌安全产品
-
即日—12.20点击申报>> 维科杯·OFweek 2024(第三届)储能行业年度评选
-
即日-12.20立即参评>> 维科杯·OFweek 2024锂电行业年度评选
-
即日-12.26火热报名中>> OFweek2024中国智造CIO在线峰会
发表评论
请输入评论内容...
请输入评论/评论长度6~500个字
暂无评论
暂无评论