化学电池行业深度报告:缘起,挑战与机遇(中)
b.中期(3-5年),富锂锰基、高电压正极等更满足比能要求,但需克服其他组分匹配问题。中期路线主要引入了Mn及其氧化物,包括富锂锰基、镍锰酸锂(LNMO)、磷酸锰铁锂LMFP等。
富锂锰基材料可以看作是由Li2MnO3(LMO)与NCM两种层状结构复合而成的材料。“富锂”指该材料相比传统正极材料,能可逆地脱嵌出更多的锂,因而具有高的理论比容量(280→320~350mAh/g),且成本与LFP接近。但由于富锂锰基结构复杂,增加了材料机理研究的难度,同时倍率、安全性及循环性能差,阻碍了商业化应用。另外,富锂锰基材料虽然具备4.5V高电压平台,但工作时阳离子易迁移及发生重排,导致晶格塌陷,进而电压发生一定程度的下降。
LMFP通过掺杂Mn到LFP内形成,具备4.1V高电压平台。但由于Mn3/4价阳离子氧化还原电位在4V左右,与电压平台接近,导致Li+嵌入和脱出时Mn3/4价阳离子发生氧化-还原反应,使得晶体结构变化,电池循环性能下降。
LNMO基于LMO发展而来,Ni与Mn含量1:1时形成的LNMO具备4.7V高电压平台,且比容量与LCO相近,使得理论能量密度超过500Wh/kg。同时由于电压平台高于Mn离子氧化还原电位,无LMFP结构变化问题,材料循环稳定性较好。但由于制备过程中内部存在大量锂镍混排以及较多杂质,实际难以获得高的电池活性,增加了产业化难度。目前商用LNMO产品有蜂巢能源的NMx系列。
c.长期(8-10年),正极无锂化,将对传统电池体系带来革新。在上文“性能主线”部分我们提到能量密度上限由物质理化特性决定,理论层面正极的最高阶是无锂正极,即元素周期表右上方元素(电化当量小、电极电位高),如F、Cl、O、S等。该类元素作为正极具备高比能,还因其能通过可逆化学转换反应机理与金属锂负极发生反应(而非传统的嵌入脱出机理),相关转化反应下可充分利用材料所有的化合价,因而循环过程交换电子多,电池电压高。根据热力学计算筛选出低成本、低毒、比能>1200Wh/kg的部分无锂正极有过渡金属氟化物、硫化物和氧化物。以现有电池工艺和固态电解质技术,电池能量密度预计可达1000-1600Wh/kg和1500-2200Wh/L。
在无锂正极产业化之路上,硫基正极因高比能低成本(指单质硫成本)成为开发热点。经统计,2009-2020年2月,全球与锂硫电池相关的文章发表数量突破5000件以上,主要由中国、美国和韩国贡献。但锂硫电池的研究结果更多停留在实验室层面,一方面是电池循环性等性能指标较差,研发工作还远未结束。另一方面是产业化面临成本控制及工艺积累的挑战,
3.1.2负极:提高比容量
负极是储锂主体,选用时遵循比容高、电势低、循环性能好、兼容性强、稳定性好与价格低廉等原则。
1)负极材料的应用现状:目前应用最广的负极材料为碳系负极,包括天然石墨、人造石墨与无序碳等。碳系材料的储锂机制为嵌入型,即材料微观结构具备一定的冗余空间,锂离子通过嵌入脱出来完成充放电循环过程。
碳基材料种类较多,差异主要体现在比容与首次效率:天然石墨成本低,但首效与倍率性能稍弱,主要应用于消费类电池。人造石墨通过前驱体、改性等工序改善了天然石墨的表面缺陷,开始规模化应用于动力电池,出货量占所有负极材料比例已超80%。
钛酸锂储锂机制同碳基材料,目前有小规模应用:钛酸锂(Li4Ti5O12)为尖晶石型构造,循环稳定性高,安全性能优势突出,但也有克容量低、倍率性能差等劣势,且成本较高,在公共交通领域有一定应用。
负极材料性能参数对比
2)负极材料发展趋势:我们预计在短期内,碳材料仍然是重要的负极载体。未来中短期以至长期,基于不同的储锂机制,碳硅负极,硅负极,金属锂负极将开始尝试应用,其可用性一方面依赖自身的技术进步,同时也需要其他体系如正极,电解质的同步迭代来配合支撑。
负极材料储锂机制分为3种类型,包括嵌入型、合金化型和转化型。嵌入型负极材料通过将锂离子嵌入其层间隙进行储锂,合金化型负极材料通过与锂离子发生合金化反应进行储锂,转化型负极材料通过与锂离子发生可逆的氧化还原反应进行储锂。
不同负极储锂机制示意
来源:Wang, Jiangyan & Tang, Hongjie & Wang, Huan & Yu, Ranbo & Wang, Dan. (2017). Multi-shelled hollow micro-/nanostructures: Promising platforms for lithium-ion batteries. Mater. Chem. Front.. 1. 10.1039/C6QM00273K.
碳系材料储锂机制为嵌入型,比容上限~372mAh/g,现有市场高端产品已达360-365mAh/g,接近理论上限。此外,碳系材料嵌锂电位0.05V,循环时难以解决锂枝晶问题。负极行业替碳需求驱动较强。
硅基储锂机制为合金型,比容上限提升可达11倍。由于新生成的合金化合物体积增大,在循环时会造成负极材料的膨胀与收缩(320%形变,对应碳基仅12%),进而影响循环稳定性甚至负极失效。另外硅基与其他材料也存在耦合问题,导致其导电性及初始活性等性能也较差。总体上便阻碍了硅基材料的应用。
为解决上述问题,产业层面对硅基负极进行了改性处理,针对性解决1)膨胀问题:硅氧化、纳米化;2)首效问题:预锂化、补锂添加剂;3)膨胀、导电与活性的综合问题:复合化(主要是碳硅复合)、多孔化、合金化。
长期来看,金属锂负极因高比容低电位而具有应用潜力,但还需要较长时间解决其固有缺陷,如锂枝晶带来的安全风险等。产学界预测在中短期内,金属锂负极还是以示范、细分领域应用为主,未来5~10年内渐进式演进后逐步进入动力电池领域。
3.1.3电解质:耦合电极体系优化。
目前电解质为有机液态,主要由溶质、溶剂及添加剂组成。因下游需求不同形成多元的电解质产品。主流电解质产品基本定型,短期内贴合下游应用场景变化进行针对性改良;长期将完成由液态、半固态到固态的转变,大幅提升电池安全性。
1)电解液应用现状
溶质:成分为锂盐,核心参数主要有离子迁移率、离子对解离能力、溶解性、热稳定性等。当下LiPF6(简称“六氟”)是主流溶质产品,成膜性能较优、电化学窗口宽且污染小,但也具有低温下易结晶、热稳定性差且对水敏感等缺陷。当前正在开展LIFSI(简称“双氟”)的应用尝试,双氟温区大于六氟,且循环寿命、放电倍率及安全性更好。
溶剂:主要为酯类有机物,主流溶剂有环状碳酸脂(TFPC、PC、EC)、线性碳酸脂(DMC、DEC),新型溶剂有羧酸酯、亚硫酸酯等。其中环状碳酸脂类溶剂介电常数很高,粘度较大,线性指标相反。由于单一材料各有优劣,应用时一般混合多种溶剂使用。
添加剂:局部改善电解液性能。根据用途可分为为成膜添加剂、电解液稳定剂、阻燃添加剂、导电添加剂、防过充添加剂和其他添加剂等。成膜添加剂应用普遍,其主要功能为在首次充放电时可率先在负极形成SEI层,从而改善电池性能。
2)电解质发展趋势:全固态锂电池技术趋势下,电解质将逐渐完成液态、半固态、固态的转变。固态电解质具备高电化学稳定窗口(5V以上)、高机械强度、阻燃性高、不挥发、易封装等优点,可大幅提高电池能量密度及安全性。但应用挑战在于固态形式下,电解质导电率低,界面阻抗高,产学界往往采用渐近式路线开发。
固态电解质分类:当前研发方向主要有聚合物型(polymer)、无机型(inorganic)、和有机-无机复合型(composite)三种。其中1)聚合物型:由聚合物基质和锂盐组成,相比于无机型柔顺性、成膜性更好且质量较轻,但导电率更低;2)无机型:主要有氧化物、硫化物两类。氧化物路线导电率、电化学窗口较高,但需要额外包覆等工序防止其被Li还原;硫化物电导率相对更高,且更易加工,但硫本身易被氧化,导致其电化学窗口窄,生产环境要求高;3)有机-无机复合型:在聚合物型内添加无机粒子(提高导电性能)。
固态电解质类型及性能参数
来源:Zhu, Xiaoqi & Wang, Kai & Xu, Yanan & Zhang, Gefei & Li, Shengqiang & Li, Chen & Zhang, Xiong & Sun, Xianzhong & Ge, Xingbo & Ma, Yanwei. (2021). Strategies to Boost Ionic Conductivity and Interface Compatibility of Inorganic - Organic Solid Composite Electrolytes. Energy Storage Materials. 36. 10.1016/j.ensm.2021.01.002.
3.1.4隔膜:更轻薄、稳定
隔膜是隔离正负极(防止短路)且保证离子正常通过的聚合物薄膜。其性能直接影响电池安全性,同时一定程度上影响能量密度、循环性能、充放电电流密度等指标。膜材料产业十分成熟。中短期内主要进行轻薄化迭代,同时配合电池功率的提升对应开发耐高温材料。长期存在被固态电解质替代可能性。
1)隔膜应用现状:目前商业化膜材料以聚烯烃为主,包括聚丙烯(PP)、聚乙烯(PE)、聚丙烯和聚乙烯复合材料等。隔膜行业上游材料为主流化工产品,产品性能受工艺影响较大(而非材料本身)。其中,加工工艺分为干法和湿法两类,其中湿法隔膜一致性、强度等指标优异,主要应用于中高端电动汽车、中高端消费电子等领域。
湿法隔膜:湿法隔膜生产工艺更复杂(技术门槛高)、成本更高。需要先通过混合-萃取制备储基膜(热稳定性与吸液性较差),再进行涂覆处理,包括有无机-有机复合改性、有机-有机复合改性两类路径。由于多种材料不同排列组合后产品性能各异,因此实际生产时往往会将不同浆料进行混合涂覆,核心knowhow体现在浆料配方及混合配比中。
2)隔膜发展趋势:在保障安全性的基础上,隔膜一方面将进一步趋于轻薄化,以提升能量密度。另一方面将开发热稳定性材料,以满足高功率动力电池对安全性的要求。长期来看,液态锂电将长时间存在,半固态电池仍需隔膜应用。未来5~10年内固态电池取得颠覆性进步后,在部分场景下将不再需要隔膜。
3.2工艺层面:材料规则下的边际改善
工艺技术迭代是在既定材料体系约束下的一个边际改善的过程。电池生产制造流程环节众多,各环节工艺优化需要遵循底层材料原理,同时与环节上下游进行耦合、适配。
电芯制造是电池工艺的核心,核心挑战为高效高一致性的产出。电芯生产环节主要可细分为前中后三段流程。
1)前段工序:极片制造过程。对生产环境要求高,需要控温、控湿、无尘。其中最关键环节为涂布工序,即将搅拌后的正负极材料均匀地涂在金属箔片上并烘干成正、负极片。涂布工序核心设备为涂布机,其涂布速度、涂布重量与厚度的一致性、涂层与基层的粘接性直接影响电芯性能。
核心涂布技术:分为干法、湿法两类。干法在提效降本的同时,还能兼容下一代材料技术,应用潜力较大,但限于极片脱粉与专用设备匹配问题,干法技术未规模化推广。
湿法技术:通过粘合溶剂对电极粉末进行粘结、涂覆、烘干,需要配备价格昂贵的电极涂布机,且溶剂有毒且难回收。
干法技术:以特斯拉Maxwell干法技术为例,主要分3个流程(粘结剂与电极粉末混合、挤出成膜、热压成型)。由于干电极具有更高的压实密度,同时更易于负极补锂,因此可以较大提高电池能量密度(已实现300Wh/kg,目标500Wh/kg)以及提高循环寿命(~2倍)。同时,由于省去了溶剂材料及涂布、烘干等工序,理论降本10~20%。另外,干电极对高镍正极、硅基负极等新型材料体系有较好的适配性。高镍正极对湿度、粘结剂敏感,干法适配性较好;硅基负极预锂化过程中体积膨胀,干法相对承受能力更强。
2)中后段工序:极片装配与电芯封装过程。中后段工序的核心流程为将极片、隔膜压实整合形成电芯主体,该流程影响电芯产出的一致性,主要分为卷绕与叠片两种路径,各有优缺点及工艺优化空间。
卷绕:顾名思义,即将极片与隔膜通过卷绕的方式整合。卷绕技术成熟,效率高,符合产业初期规模化扩张需求。但卷绕过程中,电芯存在多处弯折区域和集流体焊接区域,一方面使得内部空间利用率低,并且会有卷绕张力的不均匀和形变等现象。方形和圆柱电池适用卷绕。
卷绕工艺示例
来源:央视财经
叠片:典型为“Z”字形叠片(也有卷绕式叠片),即让隔膜以“Z”字形穿行的同时,在其两侧分别叠加正负极极片。虽然叠片技术相对卷绕更新,过程中新增的虚焊、极片毛刺、粉尘等问题还需要解决,但叠片技术对能量密度、循环及安全性有提高,符合电池渐进式演进的需要,因为行业内部也在积极进行尝试。方形和软包电池适用叠片。
叠片工艺示例
来源:睿站
封装:电池有方形、软包和圆柱三种外形。其中1)方形电池采用钢或铝合金外壳,兼容叠片及卷绕工艺,生产技术成熟;2)软包电池在方形外观上叠加了聚合物外壳(铝塑膜),同时采用叠片工艺,相对提高了安全性和能量密度,但成本也更高;3)圆柱电池采用钢或铝合金外壳,工艺层面的高度成熟使得电池一致性和自动化程度高。
3.3结构层面:提高能量单元占比
结构创新是在材料体系约束下的渐进式革新。传统电池结构为三级结构,即“电芯cell-模组module-电池包pack”。在既定的材料体系下,电池结构创新主要在电芯与系统两个层面开展。其中,电芯层面的结构创新是基础,主要围绕提高安全性、一致性与空间利用率目标进行。而电芯品质的提升降低了部分辅件系统价值,进而支持了系统层面的集约化改进。
结构创新的核心驱动为增加电池系统的实际带电量。车载场景内车辆底盘空间有限,整个电池系统需要尽可能多地提高功率组件(电芯)占比,未来动力电池系统将向大尺寸模组、无模组方向发展。
车载动力电池模组结构演进
1)电芯结构优化:基于电池现有的封装方式,电芯层面在方形和圆柱路线上均有结构创新落地,具体体现为方形路线下的长电芯方案与圆柱路线下的大圆柱方案。
刀片电池外形
来源:比亚迪官网
大圆柱方案:以特斯拉发起的4680电池为代表。核心逻辑也是减少辅助结构件,但4680通过做大单体电芯,减少了电芯数量并增大了电芯支撑力,进而减少电池辅件。同时4680采用无极耳结构,使得电子运动距离大幅缩短,内阻减少,带来更高的能量密度(300Wh/kg)、输出功率(峰值1000W/kg)与更好的快充性能(15min0-80%)。
4680结构展示
来源:特斯拉官网
2)系统结构优化:系统结构的创新整体体现出大模组化、去模组化、集成化的特征。主要思路是在系统集成过程中去掉冗余的零件,优化功能设计,进而降低工艺复杂度,节约材料使用,最终将电池与整车进行整合集成。早期电芯在单体层面一致性稳定性差,采用“电芯-模组-电池包”三级架构可以增强电池安全性、降低生产及维修成本。随着单体电芯品质提升,能量密度提升与降本需求驱动电池去模组化,与整车集约化。就具体技术而言,主流路线可以分为Cell to Pack(CTP),Cell to Chasis(CTC)两大类。
CTP技术:
宁德时代:从2019至2022年7月已迭代3次,电池空间利用率从55%提升至72%,目前已完全取消模组,转而用集约化的多功能夹层替代。该夹层兼具液冷、支撑、缓冲功能,提高了电池散热效率与热管理反映时间,在保障安全及寿命情况下更好适配4C快充。对应三元系统能量密度≥255Wh/kg(超过4680~13%),铁锂系统≥160Wh/kg。
比亚迪:在刀片电池基础上,对应不同尺寸的长电芯出具不同CTP方案,体积比能最高可增加32%。
CTC技术:即将电池与EV内三电系统、底盘、整车等进行统一整合。
宁德时代:将电池重新布置的同时与三电系统集成,统一通过智能化动力域控制器优化动力分配和降低能耗,使得成本下降,重量减轻而提升续航(800-1000km),乘坐空间更大。CATL预计2025年前后推出高度集成化CTC技术,2028年前后有望升级为智能化CTC电动底盘系统。
原文标题 : 化学电池行业深度报告:缘起,挑战与机遇(中)
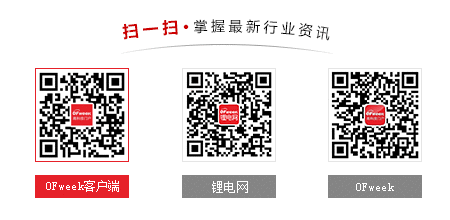
图片新闻
最新活动更多
-
限时30天免费下载>>> 《村田中国-智能驾驶感知器件应用指南》
-
9月24-25日观看直播>> 2024中国国际工业博览会维科网·激光VIP企业展台直播
-
9月30日立即试用>> 【有奖试用】爱德克IDEC-九大王牌安全产品
-
10月22日立即预约>> 【电力运营直播】主动预测维护如何提高电力运营稳定性?
-
11月14日抢先报名>> 【在线峰会】OFweek 2024固态电池生态大会
-
即日-11.30免费预约申请>>> 燧石技术-红外热成像系列产品试用活动
发表评论
请输入评论内容...
请输入评论/评论长度6~500个字
暂无评论
暂无评论